CNC Drilling in Automotive Manufacturing: Enhancing Structural Integrity and Safety
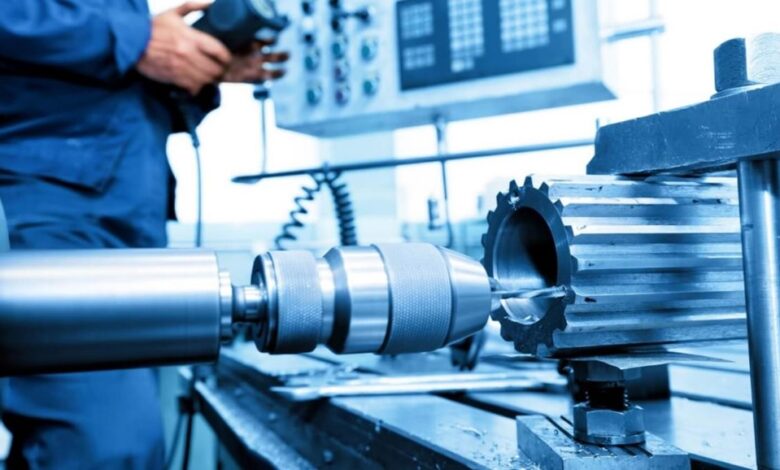
The automotive industry relies on precision, efficiency, and consistency to produce vehicles that meet stringent safety and performance standards. CNC drilling plays a pivotal role in achieving these goals, particularly in creating precise holes for assembly purposes in key components such as automotive frames, suspension systems, and exhaust systems.
By ensuring accuracy and repeatability, the CNC drilling service contributes to the structural integrity and safety of vehicles, ultimately improving their performance on the road.
The Role of CNC Drilling in Automotive Manufacturing
CNC drilling technology is designed to deliver precise, controlled drilling operations across a wide range of materials, from lightweight aluminum to hardened steel. In the automotive industry, these materials are often used in critical components that must be securely fastened together for the vehicle to function safely and efficiently.
Key Applications of CNC Drilling in Automotive Components
1. Automotive Frames
The frame or chassis of a vehicle forms its backbone, providing structural support and distributing loads across the entire structure. CNC drilling is essential in creating precise holes for the assembly of various frame components, such as cross members, pillars, and rails.
The accuracy of these holes ensures that fasteners, bolts, and rivets are securely anchored, preventing misalignment and ensuring optimal strength. High-precision drilling also helps maintain the vehicle’s structural integrity during collisions, thereby enhancing occupant safety.
2. Suspension Systems
The suspension system is crucial for the smooth handling and stability of a vehicle, absorbing shocks and maintaining tire contact with the road.
CNC drilling ensures the precise placement of holes for the mounting of suspension components, such as control arms, springs, and shock absorbers. Misaligned or inaccurately drilled holes can lead to premature wear, instability during driving, and compromised vehicle safety.
By improving the alignment and fit of suspension parts, CNC drilling enhances the overall performance and longevity of the suspension system, leading to safer driving experiences.
3. Exhaust Systems
Exhaust systems play a vital role in directing harmful gases away from the engine and the vehicle’s interior, while also minimizing noise and enhancing fuel efficiency.
CNC drilling is used to create holes for mounting brackets, flanges, and sensors, ensuring the proper assembly of exhaust pipes, catalytic converters, and mufflers.
Precise hole placement contributes to a tight seal between exhaust components, reducing the risk of leaks that can negatively affect engine performance and vehicle safety.
How CNC Drilling Improves Vehicle Safety and Performance
The precision offered by CNC drilling is not merely a matter of convenience—it is essential for ensuring that vehicles meet rigorous safety standards and perform reliably under various conditions.
Here’s how CNC drilling enhances vehicle safety and performance:
1. Enhanced Structural Integrity
Accurate hole placement in key components ensures that the parts fit together as designed, minimizing the risk of structural failures.
Whether in the chassis, suspension system, or exhaust, securely fastened parts help maintain the vehicle’s rigidity and strength.
This structural integrity is particularly critical in the event of a collision, where a vehicle’s ability to absorb and distribute impact forces can make the difference between life and death.
2. Improved Durability and Longevity
CNC-drilled holes are highly precise, reducing the chance of misaligned or loose parts that can wear down over time.
This accuracy helps prevent premature component failure, reducing the need for frequent repairs and replacements. For example, in the suspension system, precisely drilled holes ensure a tighter fit between parts, reducing unnecessary movement that could lead to wear and tear.
This not only prolongs the life of the components but also improves the vehicle’s overall safety and reliability.
3. Consistency and Repeatability
In mass production, this consistency is essential to guarantee that every vehicle rolling off the assembly line adheres to the same safety and performance standards.
CNC machines are programmed to maintain tight tolerances, ensuring that each drilled hole is identical to the next. This repeatability eliminates variability, which is critical when assembling high-performance and safety-critical components like suspension systems or automotive frames.
4. Reduced Human Error
CNC drilling also minimizes the risk of human error, which can be prevalent in manual drilling processes.
By automating the drilling operation and following pre-programmed instructions, CNC machines ensure a higher level of accuracy and consistency than manual methods.
This not only improves safety by reducing the chance of faulty components but also enhances productivity by speeding up the manufacturing process.
The Future of CNC Drilling in Automotive Manufacturing
As the automotive industry evolves, particularly with the emergence of electric vehicles (EVs) and advanced driver-assistance systems (ADAS), the demand for precision manufacturing will continue to rise. CNC drilling will play an even greater role in producing components that are lightweight, durable, and safe.
The use of advanced materials, such as carbon fiber and high-strength alloys, will require even more accurate and sophisticated CNC drilling techniques to maintain structural integrity without adding unnecessary weight to the vehicle.
Additionally, with a growing focus on sustainability, CNC drilling is increasingly becoming more environmentally friendly. Modern CNC machining services are designed to be energy-efficient and generate less waste compared to traditional manufacturing methods, aligning with the automotive industry’s commitment to reducing its environmental footprint.